财富500强企业富士康科技集团1974年成立于台湾,业务范围涵盖消费性电子产品、云端网络产品、计算机终端产品、元件及其他等四大产品领域,在20多个国家及地区设有生产及服务基地。近年来,富士康积极投入“电动车、数位健康、机器人”三大创新产业以及“人工智能、半导体、新世代通讯”三大核心技术领域,以“3+3”结合作为集团重要的长期发展策略,为全球标杆客户提供完整解决方案,成为全方位智慧生活提供者。
7月25日,在西门子召开的“2024大中华区Realize LIVE用户大会”精益制造分论坛上,富士康科技集团数字化项目负责人林建权重点阐述了集团在智能制造领域的创新和成就,特别强调了仿真和数字孪生工厂(metafactory)的重要性,并提出智能制造应全面朝向数字化转型,应用人工智能、VR/AR等先进技术。他详细介绍了富士康在仿真和智能仓库等方面的成功案例,展示了如何通过仿真技术优化生产流程和提升效率。同时也提到了携手西门子等国际伙伴瞄准建立数字孪生工厂的目标,致力于实现从设计到生产的全过程数字化和智能化改造,进而推动智能制造的发展。最后他提出精益化与智能化双螺旋模型将相辅相成,共同推进未来工厂的发展。
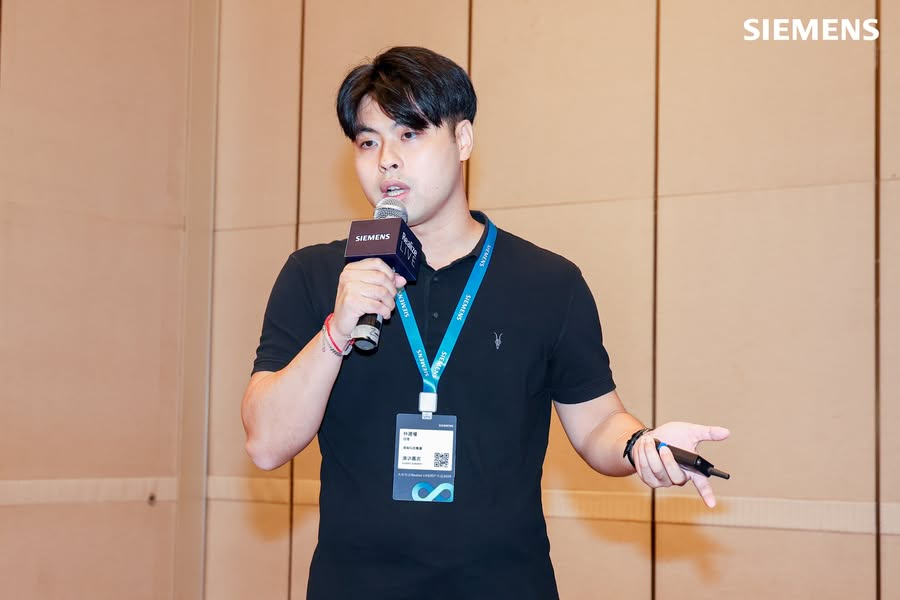
以下内容根据演讲整理,未经本人及主办方审定。
智能制造概念已经提出已久,不少企业已经积累了丰富的实践,但也有不少企业还停留在20年前的自动化水平。富士康科技在推进集团整体智能制造的基础上,深入开展精益化建设,针对单点应用进行改善,逐步实现全面的数字化应用与转型。
2024年,富士康智慧工厂建设关注的重点技术正在从人工智能、先进自动化、数字孪生、灯塔工厂、绿色环保、以人为本、数字平台转向Gen AI、人型机器人、仿真模拟、可再生能源、人机协作、开放架构、云计算等并举及深化应用阶段。
仿真应用是富士康今年的一项重点工作。富士康致力于借助诸如仿真、人工智能自动化等先进技术,逐步构建具有高度实时性和灵活性的数字孪生工厂,推动智能制造的全面发展。
仿真应用四步走
仿真技术主要是通过计算机模拟物体或系统的行为和性能,帮助预测和优化设计方案。它是一种离线模拟,虽然能够提供对物体或系统的理解和优化,但不具备数字孪生的实时性和闭环性特征;基于仿真技术的数字孪生,通过集成其他新技术,实现更高级别的实时性、闭环性和优化功能,是实现从数字世界向物理世界连接的关键。
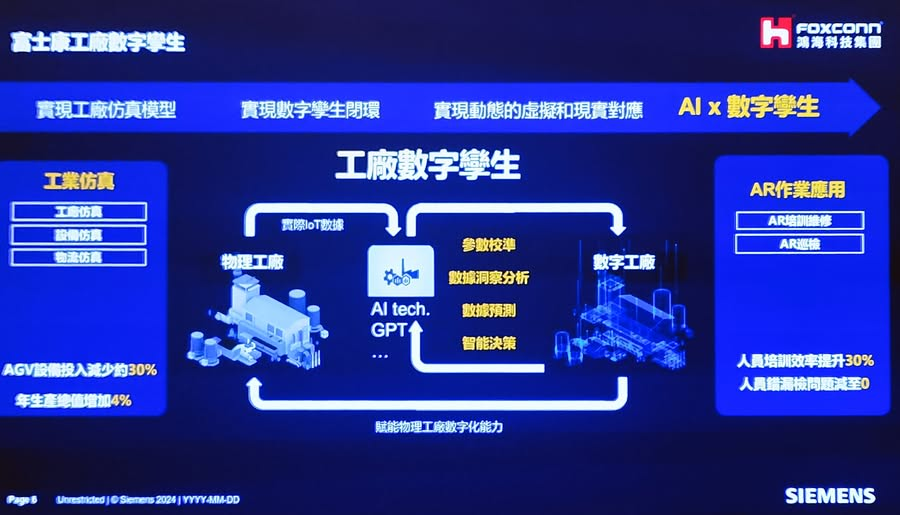
在富士康,数字孪生重点关注真实生产运营与生产数字孪生、真实产品运营与产品数字孪生,并采取四个步骤来推动和建设数字孪生工厂(metafactory):
一是采集各类数据,建立一个基于工厂、所有设备以及物流业务在内的真实数据的仿真模型,实现虚拟与现实之间的数据传输。对应的效果是,AGV设备资金投入减少约30%,年生产总值增加4%;
二是把数据赋能到模型中,实现数字孪生的闭环。但这个程度上,数字孪生还不足对生产制造产生体量;
三是做到动态的虚拟现实映射,实现真正意义上的数字孪生,对制造流程相关及以外的实际IOT数据、参数校准等更多层次的业务提供及时的响应和支持。以AR培训维修和AR巡检应用为例,其人员培训效率提升30%,人员错漏检题降低至零;
四是结合AI技术(如GPT)的应用,让数字孪生工厂具备更强的数据洞察力、预测能力和智能决策功能。
这四个步骤体现了富士康和鸿海精密一些项目的效果。
通常情况下,要构建一个全新的制造工厂,生产产线和流程往往成本很高很复杂,而仿真方法提供了一种在部署前研究造流程和系统行为的方法。富士康的仿真方法是分成设备层、产线层、工厂层三个模块来进行,简单来说就是从点到线到面,其优势是,在设备层,可完成控制逻辑验证,缩短设备调试时间;在产线层,实现物料流及吞吐量验证,物料运输和产线物流量化,提供设备综合效率(Overall Equipment Effectiveness)分析报告;在工厂层,可优化布局,验证生产策略,完成生产控制和布局的备选方案验证。
数字孪生工厂搭建完成之后,富士康又从整个工厂范围采取回头再细化到产线到设自动化单元,再到设备的方式,实现仿真工厂的落地。
推进仿真工厂全面落地
富士康仿真技术已成功应用于多个层级,包括设备、生产线乃至整个工厂。
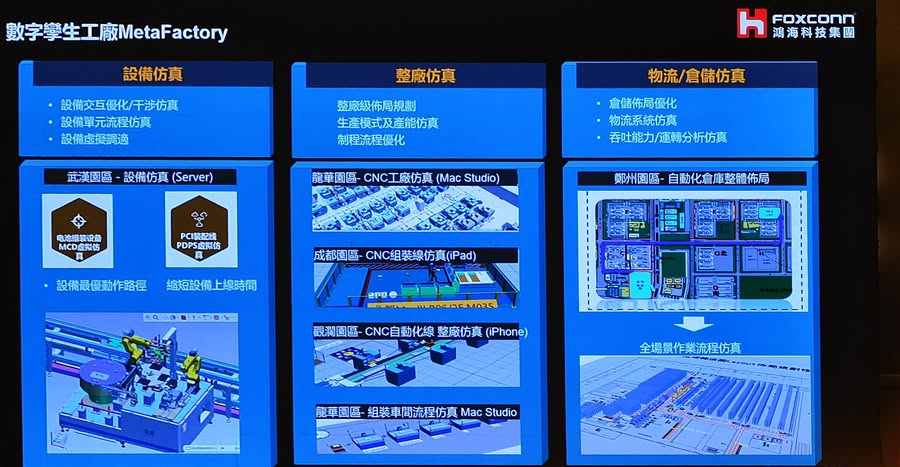
在设备方面,富士康采用NS的MCD做了一些虚拟仿真调试,用PDPS做了一些设备的虚拟仿真调试等。
在整厂仿真方面,富士康在龙华园区、成都园区以及观澜园区等各地CNC工厂分别实现了组装、自动化产线的整厂仿真应用。整厂仿真也是富士康符应用最多的场景。
在物流仓储方面,富士康在郑州园区支持了全场景作业流程仿真,实现对自动化仓库的整体布局。
这些应用普遍取得了理想的成效。
富士康CNC工厂主要从事数控机床加工相关工作。在CNC工厂优化和改进过程中,富士康采用了西门子工业软件的仿真软件Simulation支持CNC设备、HV、手臂等的运转,以及针对整个皮带线和CNC设备实现更好的搭配,产生了一些实际的效益。
基于Simulation成功应用的基础之上,富士康正在推进数字孪生,后期将把数据接进来做一些看板,然后在VR上进行开发并通过VR展示实时连线状态和数据分析结果,实现真正意义上的数字孪生。
林建权现场演示了两个仿真应用场景。
在以跟随视角的漫游产线内的仿真场景演示中,点击“数据看版”按钮,打开资料,看板两侧就展示实时生产动态、生产分析、设备状态、换刀分析、品质动态、品质分析、入库分析、人力分析等看板资料,还可放大查看。
在另外一个完整智能仓场景的仿真中,富士康展现了一个灯塔工厂包括分货、理货、倒箱、料箱入库作以及叉车运转、IQC按指令抽选料等主要的作业流程。富士康针对整场物流自动化方案,按照若干大区块完成了一次完整的Simulation。通过对整场物流的吞吐量能否达到计划需求、各个区域的运转情况是否正常、有否存在卡点,进而查找和分析、判断其原因,做必要的改善。
数据驱动的孪生工厂
截至去年,富士康完成了大量的仿真项目。今年富士康还将针对各个集团内各地的需求继续跟西门子持续在合作推进仿真项目。
西门子规划的数字主线其实放在鸿海精密及富士康一样。除了借助西门子Simulation建设数字孪生工厂之外,富士康确定了一个目标(数据驱动的智慧制造,打造孪生工厂)与6大数字主线(产品、模拟、工艺、IIOT与制造、电子装配、多业态),通过加强西门子的继续合作,应用Teamcenter等其他更多产品和解决方案,构建一个全流程的数字孪生工厂。
双股螺旋发展模式推进未来工厂建设
从最早精益数字化工厂,到后来用仿真做一些项目来验证、虚拟调试,富士康希望能结合AI进来做一个全流程的数字孪生工厂建设。实现更接近认知上的智能制造。
未来工厂应该是怎么样?
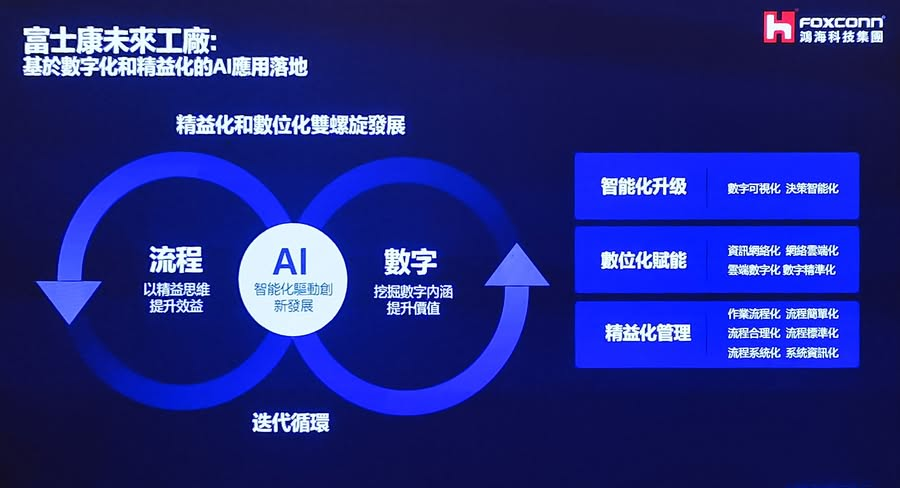
林建权认为,未来智能工厂并不只是精益化、自动化、数字化单独推进的脉络,而应该是螺旋式上升的发展态势。富士康在利用各类先进技术建设孪生工厂继续推进数字化建设的同时,还将运用精细化思维在生产管理中,通过精益化的思维与数字化的赋能,结合AI来智能化驱动创新,以双股螺旋的发展模式推进富士康未来工厂愿景成真。
为期两天的西门子“2024大中华区Realize LIVE用户大会”于7月24日在上海盛大开幕。作为西门子在工业软件领域的年度盛会,此次大会聚集千余位行业专家、企业代表、西门子专家以及优秀合作伙伴,开设多个论坛及产品实操培训课程,聚焦人工智能、工业元宇宙、数字孪生等技术在工业应用的新范式,探寻行业数智化发展的前沿。
【关于演讲嘉宾林建权:富士康科技集团数字化项目负责人,主要负责整个集团的数字化的应用与项目的落地】